First published in Process Industry December 2019 issue
Powder/Solids processing valves present more performance challenges than gas or liquid valves and therefore often require more consideration of available options and customization. Before we detail the two most common options, readers may find it useful to review the basic factors to consider when specifying solids processing valves here.
High Temperature Options
Soft seated valves with elastomers are typically limited to around 200C. Valves are considered high temperature when they are exposed to temperatures above this for extended periods. Some elastomers may handle momentary exposure to higher temperatures but this is generally not well defined and systems should be designed for worst case process conditions.
This is different from upset conditions where after an out of normal limits event, the process is shut down and the equipment is inspected and maintained before restarting operations.
For temperatures between 200C to 330C, FFKM (Perfluoroelastomer) O-rings such as Kalrez® 7075*1 may be used for valve body and valve stem seals. However, metal seats are recommended since soft seats will degrade and erode quickly and will not provide a reliable shut-off.
Metal seated valves have a tendency to jam as the valve heats and expands and are often set with a predefined clearance between the seat and shut-off disc at ambient temperature. Of course this affects shut-off class and is not acceptable in some applications. Spring loaded seats that allow for thermal expansion are an option in smaller sizes.
Carbon/Graphite based flange gaskets such as Flexicarb*2 are common in these applications. These gaskets are typically not reusable. Graphite stem packing such as Garlock® 1306*3 is typical for high temperature and some can go to 455C/850F in atmosphere and 650C/1200F in steam. Inconel wire reinforcing in expanded–graphite yarn is an additional option that provides more rigidity and dependability to the packing.
Extreme Temperatures
For bubble tight shut-off at extreme temperatures above 450C, static seals may be the best option. These can vary from standard ANSI or DIN flanges with gaskets and fasteners to Spider Clamps that allow for quicker mounting and removal. Cleanliness is critical to this process so seal faces and gasket surfaces need to be inspected and any contamination removed on every use.
NASA’s ISRU (In Situ Resource Utilisation) Technology Development Project for hydrogen reduction of regolith. The valves were used in ROxygen field tests on Mauna Kea, HI in 2008.
High Temperature Actuators
While some actuators are available with high temperature O-rings/seals, the preferred method is to isolate the actuator from the process temperature. This can be achieved by insulating the valve and process piping and/or providing a heat shield plate mounted between the actuator and valve. Another option is to provide a drive stem extension and add radiation fins to the housing extension to dissipate the heat.
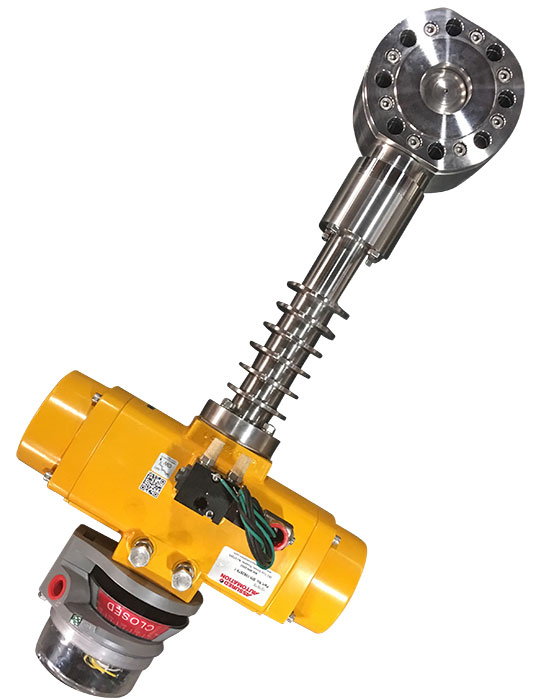
Discharge valves for vessels and processors
Flush Mount Options
Most discharge valves for vessels and processors leave a dead space where the valve mounts to the vessel. Dead space is defined as the volume between the valve shut-off element and the inside wall of the vessel. This can be an issue for mixing and processing applications where the product in the dead space remains unmixed or unprocessed.
For smaller valves – up to approximately 80mm – a mounting pad on the vessel allows the shut-off disc or ball to be close enough to the vessel to minimize the dead space to an acceptable level for most processes. This often requires the actuation package to be mounted at an angle to avoid interference with the outside wall of the vessel.
Most ball valve manufacturers offer this option. For segmented ball/spherical disc valves, angled stems are not available. Instead, an extended stem and valve mounting bracket can place the actuator outside the interference area.
As the discharge valve increases in size from 100 to 300 mm the solution is more challenging depending on the amount of dead space that is acceptable to the process.
To minimize the dead space, a mounting neck piece or pad is welded into the vessel wall and bring the diameter of the ball segment/spherical disc flush with the inside of the vessel.
However, to eliminate dead space, the ball segment and seat need to match the form of the inside of the vessel which can be flat, radius or conical. This customization requires 3D modeling and manufacturing with CNC equipment.
The geometry of the ball segment means that the shut-off disc will penetrate into the vessel as it opens and closes. If the processor has paddles, vanes, ribbons or other moving parts then interference with the ball segment needs to be avoided.
The can be achieved by interlocking the controls so the valve will not operate in the interference condition. This design and build to order comes with added costs and is only justified in exceptional applications.
Shown is a model of a retrofit, flush mount, valve design for a major producer of food ingredients who wanted to improve the mixing quality of an existing blender.
The project involved removing an existing butterfly valve and discharge cone and replacing it with a spherical disc valve and weld neck. The seat and spherical shut-off disc were manufactured to match the inside radius of the blender and eliminated the dead space.
*Gemco Valve Company mentions these brand names as examples only and receives no consideration from the owners. There are many completive products available.
*1 Kalrez® is a DuPont brand and is available in a wide range of grades.
*2 Flexitallic Industrial gaskets supplies a range of high temperature gaskets. They do state “Flexicarb will oxidize over time. Care should be taken when considering the use of Flexicarb foil for applications above 650°F (343C).”
*3 Garlock® packing is available in a range of materials and grades.