First published in Powder & Bulk Solids May 2025 issue
Before we detail the challenge of blender discharge “dead space”, readers may find it useful to review the basic factors to consider when specifying solids processing valves here.
In industries handling bulk solids, powders, or slurries, optimizing equipment design is essential to improving product quality and operational efficiency. One persistent challenge is the presence of “dead space” in the discharge zone of ribbon and paddle blenders — areas where material accumulates, stagnates, or becomes trapped. These zones lead to flow blockages, uneven mixing, and increased downtime for cleaning and maintenance.
A proven solution to this issue is the use of flush-mounted spherical disk valves. These engineered valves can eliminate dead zones by aligning flush with the internal radius of blenders, ensuring smooth flow and complete evacuation. This article explores how these valves eliminate dead space, their engineering considerations, and the benefits they bring to industrial processing.
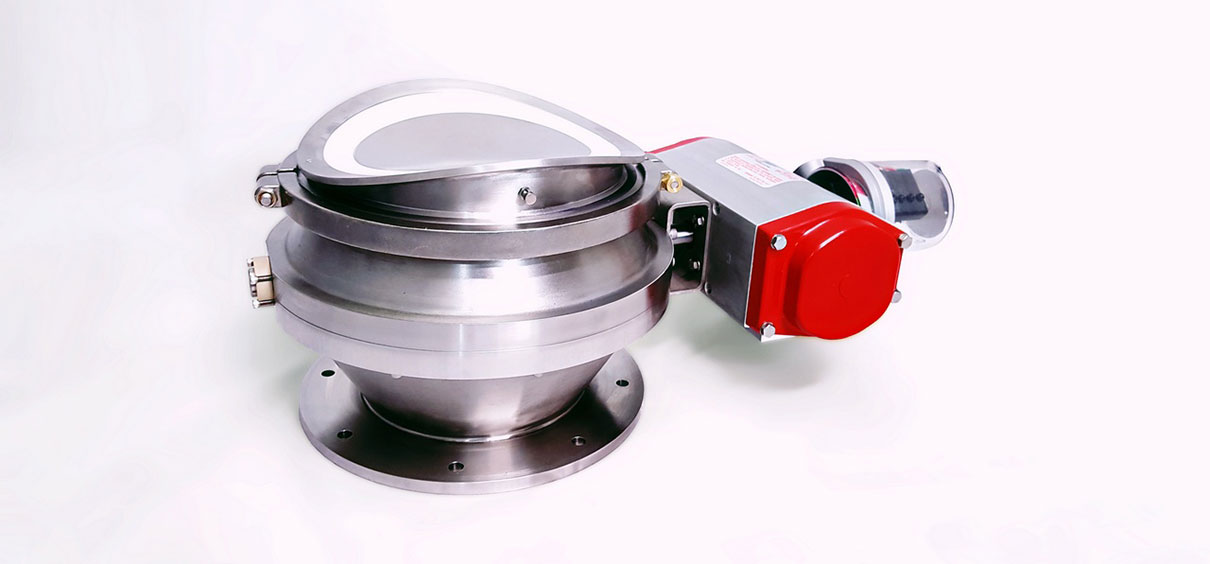
Using flush-mounted spherical disk valves is a proven solution to the dead space issue.
Understanding Dead Space in Blender Systems
What Is Dead Space?
Dead space refers to pockets within a process vessel where material movement is limited or stagnant. In ribbon and paddle blenders, these especially occur near the discharge valve, often due to mismatched geometries between U-shaped or cylindrical vessels and the attached discharge nozzles or flanges. These inconsistencies in shape and alignment interrupt the flow path and create zones that hinder efficient product movement.
While low-viscosity liquids may flow freely due to their ability to move with minimal resistance, high-viscosity slurries or powder mixtures are more prone to bridging and buildup in these areas. Over time, this can result in hardened residues, contamination between batches, and even equipment malfunction.
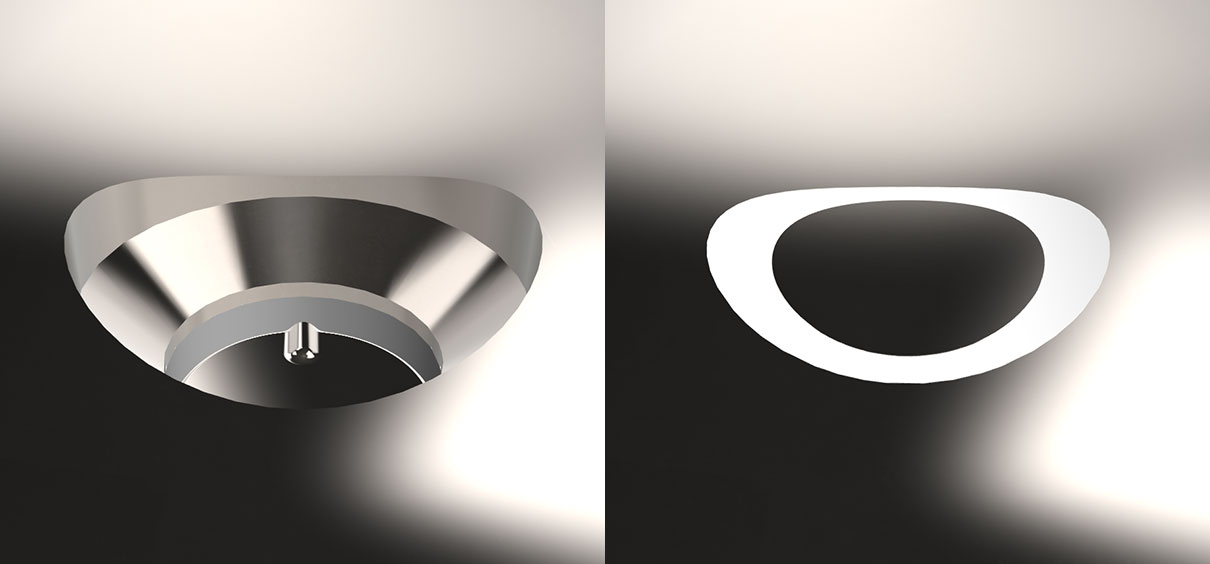
L: Blender outlet for butterfly valve; R: Blender outlet with flush spherical disk valve
Problems Caused by Dead Space
1. Incomplete Mixing
Stagnant material leads to inconsistent batch quality and poor product uniformity. This is especially problematic when handling blends that require precision, such as nutritional powders or pharmaceutical ingredients.
2. Flow Obstruction and Bridging
Solids may bridge or harden in dead zones, creating blockages and flow disruptions. Operators may need to manually clear obstructions, increasing labor and risk.
3. Increased Maintenance
Buildup in dead areas accelerates wear on internal components, requiring more frequent shutdowns and part replacements. It also introduces the risk of contamination, especially if cleaning cycles are not sufficient.
4. Cleaning Challenges
Inaccessible zones are harder to clean, increasing the risk of microbial growth and cross-contamination — particularly in regulated industries like food, beverage, and pharmaceutical.
Eliminating dead space is therefore a fundamental goal in advanced blender design and retrofitting operations.
Traditional Equipment Options and Their Limitations
Liquids
For liquid systems, bottom-outlet ball valves with low-sump (dead space) designs and weld-pad or bolt-on configurations can minimize dead zones, especially in diameters up to approximately 3 inches (80 mm). These designs work well when fluid properties ensure complete drainage through gravity or pressure-assisted systems.
However, these valves are not always scalable or effective for higher-viscosity or solid-laden slurries, which can leave behind significant residue if the valve does not conform closely to the vessel interior.
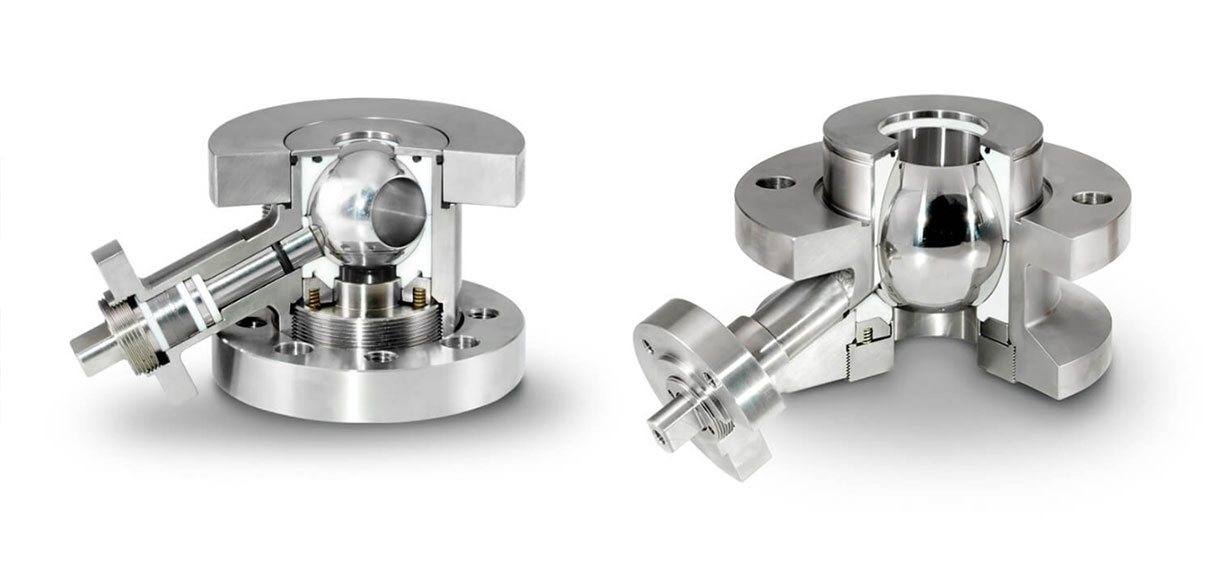
L: bottom-outlet valve with weld-on connection; R: bottom-outlet valve with bolt-on connection.
Solids
For solids systems, tank bottom T-valves with oversize flanges are used, allowing the valve to be bolted up to a pad. While this configuration helps reduce dead space, it does not fully eliminate it.
In other designs, spherical disk (ball segment) valves are mounted as close to the blender as possible but without the disk penetrating into the mixing area. Though proximity helps reduce some retention, the lack of flush mounting still results in residual volume.
For solid blender discharges, typical sizes range from 3 inches (75 mm) to 16 inches (400 mm), increasing the volume around segmented ball valves. For example, a 10-inch (250 mm) valve may have 1.25 liters of dead space, and this can increase to up to 5 liters in larger sizes. This volume may not sound significant, but in applications requiring precise dosing or cleanliness, even small amounts of leftover material can affect quality and regulatory compliance.
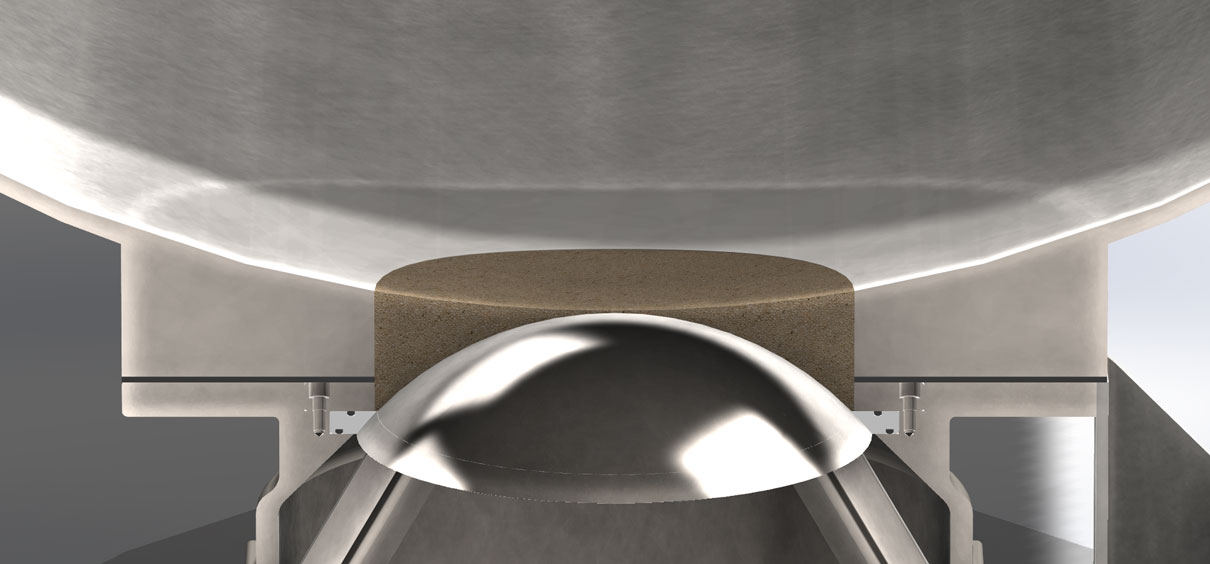
Tank bottom T valve with dead space
Introducing Flush-Mounted Spherical Disk Valves
What They Are
Flush-mounted spherical disk valves — also called segmented ball valves — feature a spherical shutoff disk with the top surface engineered and machined to fit seamlessly with the internal shape of a blender. Unlike conventional gate or butterfly valves, their geometry supports a smooth, continuous internal blender surface that enables full evacuation and minimizes hold-up zones.
How They Work
The valve’s disk rotates to open or close, typically in a 90-degree motion. Using 3D CAD/CAM engineering, the disk is contoured to match the vessel’s internal surface, allowing for flush integration. When mounted at the discharge point, the valve eliminates cavities that might otherwise trap material. As the valve opens, the disk retracts into the valve body with minimal disruption to flow, and during closure, it seals off flush with the inner wall of the vessel.
Key Engineering Considerations
Precision-shaped shutoff spherical disks match cylindrical, conical, or hybrid blender profiles. The size and geometry must be modeled to suit individual applications and equipment.
The shut-off disk penetrates the vessel during valve opening and closing. The ribbon or paddle position must be controlled with an encoder to avoid interference, and valve operation is interlocked with the mixer to ensure synchronized movement.
Retrofitting existing blenders requires an evaluation of existing connection that often needs removal and replacement, which involves cutting, welding, and polishing. Compatibility with weld pads or bolt-on adapters needs to be assessed for each application to determine retrofit feasibility.
Pressure and hygienic standards, such as ASME BPE or PED, must also be considered depending on the application. Material selection for the valve (typically stainless steel or alloy) must meet corrosion and wear requirements.
How Flush-Mounted Spherical Disk Valves Eliminate Dead Space
Seamless Flow Path
The flush-mounted design eliminates internal discontinuities that create turbulence or holdups. This ensures uninterrupted material flow and prevents buildup. In systems that rely on gravity-assisted flow, smooth transitions are critical to minimizing bridging and promoting fast discharge.
Improved Mixing Consistency
The valve’s design supports complete evacuation of material with each rotation, reducing retention zones and enhancing batch uniformity. Its self-cleaning action also helps dislodge adhering solids, reducing the likelihood of cross-contamination between batches.
Reduced Cleaning Time
Smooth, accessible internal surfaces simplify cleaning and meet stringent hygiene requirements in sensitive industries. The flush configuration reduces the need for aggressive cleaning agents or long CIP cycles, saving time and resources.
Enhanced Process Efficiency
By eliminating dead zones, cycle times are reduced, cleaning frequency drops, and productivity improves — all while maintaining consistent quality. These efficiency gains are especially valuable in high-throughput environments.
Industrial Applications
Food and Beverage
Ideal for powders, spices, and granulated ingredients, flush-mounted valves prevent cross-contamination and enable faster changeovers. In bulk ingredient handling, consistency and cleanliness are essential for flavor integrity and safety.
Pharmaceutical Manufacturing
Precise, sanitary design minimizes product retention and supports cGMP compliance, ensuring clean, reproducible mixing. Flush-mount valves reduce product loss, lower contamination risk, and align with FDA and EMA manufacturing standards.
Chemical Processing
Reduces the risk of material degradation or hazardous accumulation by eliminating stagnant zones in reactive or corrosive systems. Accurate batch control and reduced cleaning downtime contribute to better plant safety and cost efficiency.
Powders and Bulk Solids
Ensures consistent blending of dry materials and prevents blockages from powder compaction. In industries like cement, plastics, or battery material production, valve reliability and material flow are crucial to maintain throughput.
Nutraceutical and Supplement Manufacturing
In supplement production, precise ingredient blending is essential for product integrity. Flush-mounted valves ensure consistent batch quality and improve compliance with increasingly strict industry standards.
Conclusion
Flush-mounted spherical disk valves provide a modern, effective solution to one of the most pressing challenges in bulk material handling — dead space in blenders. With their tailored geometry, hygienic design, and smooth operation, these valves:
- Improve product consistency by eliminating stagnation zones
- Increase process reliability and reduce unscheduled downtime
- Lower maintenance costs by minimizing wear and simplifying cleaning
- Streamline cleaning and batch changeovers in regulated environments
As processing demands rise, especially in regulated industries, engineered valve solutions will play a pivotal role in driving operational excellence and competitive advantage. Whether integrated into new equipment or retrofitted into existing systems, flush-mounted spherical disk valves represent an important innovation for manufacturers focused on quality, efficiency, and safety.